Introduction:
A 3D-printed Torx router plate is an excellent solution for DIY enthusiasts, woodworkers, and makers who want a customized, cost-effective, and precise router plate for their woodworking projects. Traditional router plates can be expensive, but 3D printing a custom Torx router plate allows users to create a design tailored to their specific router model and needs.
In this guide, we will explore everything you need to know about 3D printing a Torx router plate, from choosing the right materials and design considerations to printing tips and installation instructions.
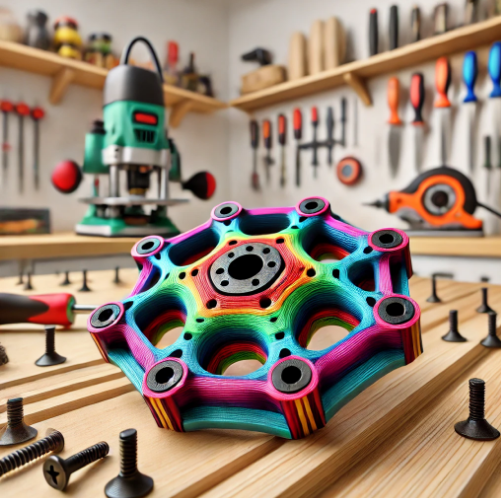
Why 3D Print a Torx Router Plate?
1. Customization
3D printing lets you customize the size, hole placement, and mounting choices to meet your particular router and workbench, unlike off-the-shelf router plates.
2. Reasonably Priced
Although a good router plate can be costly, building your own drastically lowers expenses as you only need filament and access to a 3D printer.
3. Consistency and Accuracy
Highly accurate and reproducible parts made by modern 3D printers guarantee that your Torx router plate fits exactly without calling for too many hand corrections.
4. Lightweight, Durable Materials
By choosing the correct filament—such as PETG, ABS, or Nylon—you may build a robust router plate capable of handling the strain of woodworking chores.
Choosing the Right 3D Printing Material
The success of your 3D-printed Torx router plate depends largely on the material you choose. Below are the best filaments for this application:
1. PLA (Polylactic Acid)
- Pros: Easy to print, high detail accuracy, low cost.
- Cons: Brittle under stress and heat, not ideal for heavy-duty use.
2. PETG (Polyethylene Terephthalate Glycol-Modified)
- Pros: Stronger than PLA, flexible, heat-resistant.
- Cons: Requires higher printing temperatures, prone to slight warping.
3. ABS (Acrylonitrile Butadiene Styrene)
- Pros: High impact resistance, durable, good for structural parts.
- Cons: Warping issues, requires an enclosed print chamber.
4. Nylon
- Pros: Extreme durability, great for heavy-duty applications.
- Cons: Moisture-sensitive, requires high-temperature printing.
Design Considerations for a 3D-Printed Torx Router Plate Think
About the following design issues before beginning printing:
1. Router Stability
Calculate the base of your router and make sure the plate is exactly made.
2. Thickness and stiffness
It is advised to guarantee stability and reduce flexing during use by a maximum thickness of 6mm.
3. Location of Mounting Holes
For a simple connection to your router table or workstation, guarantee exact hole alignment.
4. Torx Fasteners Slots
Combine Torx-compatible screw holes for dependable fastening.
5. Additional Characteristics
To increase use, think about including changeable inserts, dust-collecting ports, or strengthening ribs.
3D Printing Settings for Optimal Results
1. Layer Height
- Recommended: 0.2mm for fine detail and smooth surfaces.
2. Infill Density
- 30-50% infill ensures strength without unnecessary material waste.
3. Print Speed
- 40-60mm/s for a balance between speed and print accuracy.
4. Bed Adhesion
- Use a heated bed (for ABS, PETG, and Nylon) to prevent warping.
- Apply a glue stick or PEI sheet for better first-layer adhesion.
5. Supports and Brim
- Enable support if your design has overhangs.
- Use a brim or raft to improve bed adhesion, especially for ABS.
Step-by-Step Guide to Printing and Installing a Torx Router Plate
1. Create your design
- Using Fusion 360, TinkerCAD, or FreeCAD such that all mounting holes and features are included.
2. Cutting the Model
- Import an STL file into Simplify3D, PrusaSlicer, or Cura.
- Change the print settings in line with your preferred filament.
3. Printing the Router Plate
- Load the 3D printer’s filament.
- Starting the print, check the first few layers to guarantee correct adhesion.
4. Post-Processing
- For a neat finish, sand the edges.
- Drill out any mismatched holes for exact mounting.
- Before installation, test your router.
5. Router Plate Installation
- Orient the plate in line with your router table.
- Torx screws will help you to secure it.
- Verify router fit and test functionality.
READ MORE – 3D Print PSA Card Bumper – The Ultimate Guide to Protecting Your Collectibles
FAQs:
1. Is a 3D-printed router plate strong enough for woodworking?
Yes, if printed using PETG, ABS, or Nylon, your router plate will be strong enough for most woodworking tasks.
2. Can I use PLA for a router plate?
PLA is not recommended due to its brittleness and lower heat resistance.
3. How do I prevent warping when printing ABS or PETG?
Use a heated print bed (90-100°C for ABS, 70°C for PETG) and enable an enclosure to minimize warping.
4. What’s the best software for designing a router plate?
Fusion 360 is the most popular choice, but TinkerCAD and FreeCAD are also excellent free options.
5. Can I modify an existing STL file?
Yes, you can edit STL files in Fusion 360, Meshmixer, or TinkerCAD to customize hole placements or dimensions.
Conclusion:
One great approach to save money and personalize your woodworking environment is 3D printing a Torx router plate. Create a robust and accurate router plate that improves your efficiency with the correct materials, design concerns, and print settings. This guide offers all the required procedures to effectively 3D print your own Torx router plate, regardless of your level of expertise—do-it-yourself or professional.