Introduction
As 3D printing technology continues to advance, many makers and engineers are experimenting with producing custom fasteners such as 3D-printed 10mm M2 screws. These tiny screws, commonly used in electronics, robotics, and small mechanical assemblies, can be custom printed for rapid prototyping or specialized applications.
This guide will explore the feasibility, materials, design considerations, and best printing practices for creating 10mm M2 screws with 3D printing. We will also address common concerns, provide FAQs, and recommend alternatives where necessary.
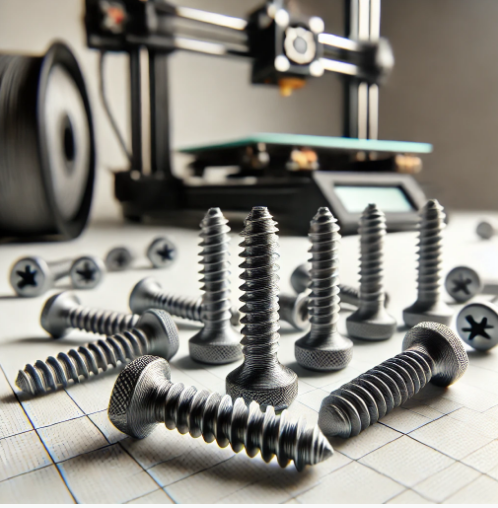
Why 3D Print 10mm M2 Screws?
1. Customization for Specific Needs
Custom thread pitches, head forms, and tolerances made possible by 3D printing let you match particular uses.
2. Quick prototyping
Testing requires a prototype fastener. Without waiting for conventional metal screws, 3D-printed screws provide immediate iterative design validation.
3. Cost Savings for Small Batches
For low-volume projects, printing your screws can be more cost-effective than ordering specialized fasteners.
4. Non-Metallic Applications
3D-printed screws are great for non-conductive, lightweight, and corrosion-resistant applications, especially in electronics and medical devices.
Best Materials for 3D Printing M2 Screws
Choosing the right filament or resin is crucial for achieving strong and functional 3D-printed 10mm M2 screws.
1. PLA (Polylactic Acid)
- Pros: Easy to print, high detail resolution.
- Cons: Brittle, not suitable for high-torque applications.
2. PETG (Polyethylene Terephthalate Glycol-Modified)
- Pros: More durable than PLA, better flexibility.
- Cons: Slightly less detailed than PLA.
3. Nylon
- Pros: High strength, impact resistance, flexibility.
- Cons: Requires high print temperatures, prone to warping.
4. Resin (SLA Printing)
- Pros: Extreme precision, great for fine threads.
- Cons: Brittle, requires post-processing, less durable under load.
Design Considerations for 3D-Printed M2 Screws
1. Thread Pitch and Tolerance
- Ensure thread depth and spacing are slightly oversized to account for 3D printer tolerances.
- Use a thread-cutting die after printing for improved accuracy.
2. Layer Orientation and Print Strength
- Print screws vertically to maximize tensile strength.
- Use at least 50% infill for added durability.
3. Screw Head Design
- Choose from hex, Torx, Phillips, or flathead designs.
- Reinforce the head with extra perimeter layers.
4. Post-Processing
- Acetone smoothing (for ABS) can refine threads.
- Tapping or thread cutting can improve fit with nuts or tapped holes.
Best 3D Printing Settings for M2 Screws
1. Nozzle Size
- A 0.2mm nozzle is recommended for fine details.
- A 0.4mm nozzle can work but sacrifices precision.
2. Layer Height
- 0.1mm or lower for high-resolution thread details.
3. Print Speed
- 30-40mm/s to prevent artifacts on small prints.
4. Infill Density
- 50-100% for maximum strength.
Limitations of 3D-Printed Screws
While 3D printing 10mm M2 screws can be useful, there are some limitations to keep in mind:
- Not suitable for high torque or load-bearing applications.
- Threads may be weak compared to metal screws.
- Dimensional accuracy is challenging without post-processing.
For permanent or industrial applications, consider metal alternatives or hybrid solutions.
READ MORE – 3D Print Torx Router Plate: A Complete DIY Guide
FAQs:
1. Are 3D-printed M2 screws strong enough for real use?
They work for light-duty applications but are not a replacement for metal screws in high-stress environments.
2. Can I print metal screws using a standard FDM printer?
No, but you can use metal-filled filament or SLS metal 3D printing for stronger results.
3. What’s the best way to improve thread accuracy?
Use a thread-cutting die or tap the printed threads for better performance.
4. Can I use resin printing for M2 screws?
Yes, resin printers offer high detail, but resin screws are brittle and not ideal for torque applications.
5. Where can I download 3D models for M2 screws?
Websites like Thingiverse, Printables, and GrabCAD offer ready-to-print M2 screw models.
Conclusion:
3D-printed 10mm M2 screws can be a great DIY solution for custom fasteners, prototyping, and specialized applications. For light-duty jobs, they provide flexibility, quick manufacturing, and cost savings even if they are not as robust as metal screws. For your projects, print settings, post-processing procedures, and appropriate materials can help you to produce exact and effective 3D-printed screws.
For mission-critical or high-strength applications, metal fasteners remain the best choice, but 3D printing opens up exciting possibilities for creative and practical solutions.